Design and development
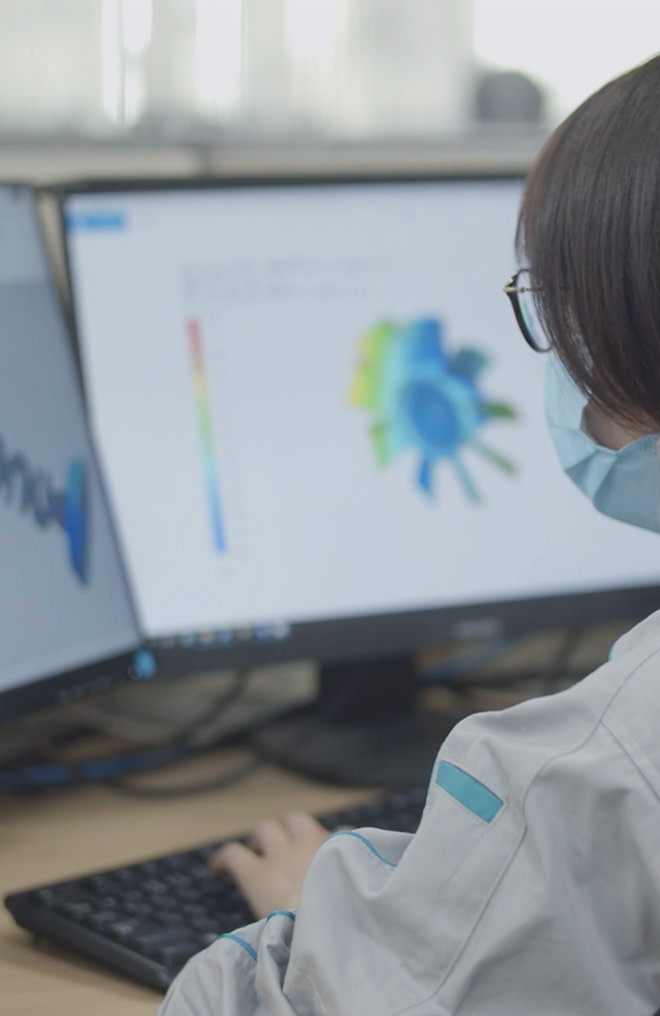
We leverage the know-how learned in our factories and introduce innovative designs to meet all customer needs
Kubota engines are a reflection of our development philosophy.
This development philosophy was born from an accumulation of product development experience and ingenuity based on perspectives not only from the industrial and construction equipment manufacturers who are our direct customers, but from the general users who are their customers as well.
Specifications, even for the same type of engine, can differ for each customer application. Requirements differ, such as power take-off positions, oil level gauge positions, and required setting outputs can all vary by customer.
But Kubota meets this challenge with flexibility by producing engines customized for each customer application with incredible speed.
This accumulation of experience and ingenuity is also revealed in design and development that produce engines with the power, quality, and durability every customer demands.
-
Design
-
-
Design and development
Design
We design engines to deliver optimum performance while meeting the specifications all our customers worldwide require based on their requirements and potential needs. Our extensive installation track record and proven technical expertise backed by verification testing ensure our engines have the durability for any application. We design high quality engines by collaborating with our casting department and incorporating knowledge from our manufacturing department in addition to applying engine development technology. We also have a group of experts developing the products in a wide range of fields such as machinery, electronics, chemistry, and physics.
-
Design and development
Workshop
The Kubota engine development team makes each engineer responsible for the bulk of development in a given area of engine development. This may also be a characteristic that distinguishes us from other engine manufacturers. Engineers conduct design and research based on information from CAD data, etc. while assembling actual engines themselves at assembly and disassembly areas in our development facilities. We work hard to improve the performance of each engine model by advancing development based on specialized knowledge and detailed data, while carefully assembling engines by hand.
-
Design and development
Test equipment
We measure exhaust emissions of designed and developed engines in our "Quality Audit Building."
In January 1995, the state of California in the US became the first in the world to enforce the "CARB ULG Exhaust Gas Regulations." To get out ahead of enforcement of these regulations, Kubota was the world's first engine manufacturer to obtain certification in 1993.
Even as emission regulations for industrial engines become more stringent, our development environment has stayed compliant with regulations in all regions of the world.
-
Design and development
Chassis dynamometer
We use a piece of equipment called a "chassis dynamometer" that mounts engines on actual applications, puts the applications on chassis rollers, and then places loads on engines that mimic loads during real driving scenarios. We check engine loads and performance based on actual operating conditions and by using wind tunnel equipment to improve the quality of engines optimized for applications.
Workshop
-
-
-
Design and development
Design
We design engines to deliver optimum performance while meeting the specifications all our customers worldwide require based on their requirements and potential needs. Our extensive installation track record and proven technical expertise backed by verification testing ensure our engines have the durability for any application. We design high quality engines by collaborating with our casting department and incorporating knowledge from our manufacturing department in addition to applying engine development technology. We also have a group of experts developing the products in a wide range of fields such as machinery, electronics, chemistry, and physics.
-
Design and development
Workshop
The Kubota engine development team makes each engineer responsible for the bulk of development in a given area of engine development. This may also be a characteristic that distinguishes us from other engine manufacturers. Engineers conduct design and research based on information from CAD data, etc. while assembling actual engines themselves at assembly and disassembly areas in our development facilities. We work hard to improve the performance of each engine model by advancing development based on specialized knowledge and detailed data, while carefully assembling engines by hand.
-
Design and development
Test equipment
We measure exhaust emissions of designed and developed engines in our "Quality Audit Building."
In January 1995, the state of California in the US became the first in the world to enforce the "CARB ULG Exhaust Gas Regulations." To get out ahead of enforcement of these regulations, Kubota was the world's first engine manufacturer to obtain certification in 1993.
Even as emission regulations for industrial engines become more stringent, our development environment has stayed compliant with regulations in all regions of the world.
-
Design and development
Chassis dynamometer
We use a piece of equipment called a "chassis dynamometer" that mounts engines on actual applications, puts the applications on chassis rollers, and then places loads on engines that mimic loads during real driving scenarios. We check engine loads and performance based on actual operating conditions and by using wind tunnel equipment to improve the quality of engines optimized for applications.
Test equipment
-
-
-
Design and development
Design
We design engines to deliver optimum performance while meeting the specifications all our customers worldwide require based on their requirements and potential needs. Our extensive installation track record and proven technical expertise backed by verification testing ensure our engines have the durability for any application. We design high quality engines by collaborating with our casting department and incorporating knowledge from our manufacturing department in addition to applying engine development technology. We also have a group of experts developing the products in a wide range of fields such as machinery, electronics, chemistry, and physics.
-
Design and development
Workshop
The Kubota engine development team makes each engineer responsible for the bulk of development in a given area of engine development. This may also be a characteristic that distinguishes us from other engine manufacturers. Engineers conduct design and research based on information from CAD data, etc. while assembling actual engines themselves at assembly and disassembly areas in our development facilities. We work hard to improve the performance of each engine model by advancing development based on specialized knowledge and detailed data, while carefully assembling engines by hand.
-
Design and development
Test equipment
We measure exhaust emissions of designed and developed engines in our "Quality Audit Building."
In January 1995, the state of California in the US became the first in the world to enforce the "CARB ULG Exhaust Gas Regulations." To get out ahead of enforcement of these regulations, Kubota was the world's first engine manufacturer to obtain certification in 1993.
Even as emission regulations for industrial engines become more stringent, our development environment has stayed compliant with regulations in all regions of the world.
-
Design and development
Chassis dynamometer
We use a piece of equipment called a "chassis dynamometer" that mounts engines on actual applications, puts the applications on chassis rollers, and then places loads on engines that mimic loads during real driving scenarios. We check engine loads and performance based on actual operating conditions and by using wind tunnel equipment to improve the quality of engines optimized for applications.
Chassis dynamometer
-
Kubota INNOVATIVE METHOD
Kubota's uniquely consistent
production system,
featuring innovations
unlike any in the world